Red light and BlueLight Comparison
What are the differences between red light and blue light sensors?
In a word, wavelength. Red light sensors use red light, which has a long wavelength. While blue light sensors use short-wavelength blue-violet light. Because the wavelengths have different characteristics,
the two types of sensor must be considered individually for each application.
Crucially, red light sensors reach their limits when detecting difficult surfaces such as dark, high-gloss, slanted, convex or transparent materials. Furthermore, their process stability decreases at strong
angles of inclination.
This is precisely where blue light sensors come into their own. Because short-wavelength blue light is less likely to be absorbed or reflected away, it enables high process stability with challenging materials and difficult surfaces, even at strong angles of incidence. Better still, they are flexible in use and can detect critical as well as non-critical objects to the point where, if needed, they can replace red light sensors, thus saving space and cost.
BlueLight goes beyond the capability of red
In a typical assembly line, red light sensors are the go-to solution. However, with the rising prevalence of dark, curved and highly reflective surfaces, not only can BlueLight technology do the same job as red light, but it can also achieve reliable detection well past the point where red light reaches its limit. This increased ability has earned BlueLight the reputation for being the new industry standard.
When would BlueLight be the ideal choice?
It is a case of ‘whatever you can do, I can do better’. Not only can BlueLight sensors perform all the tasks of red light sensors, they are perfect for a number of additional scenarios. As well as achieving reliable detection with challenging surfaces, as mentioned above, the superior reflective properties of BlueLight are effective with stronger angles of incidence, and also offer adjustable background suppression for very bright or busy environments.
Below we explore three scenarios where red light and BlueLight sensors are able to solve the same applications.
SCENARIO A: FILLING QUANTITY MONITORING
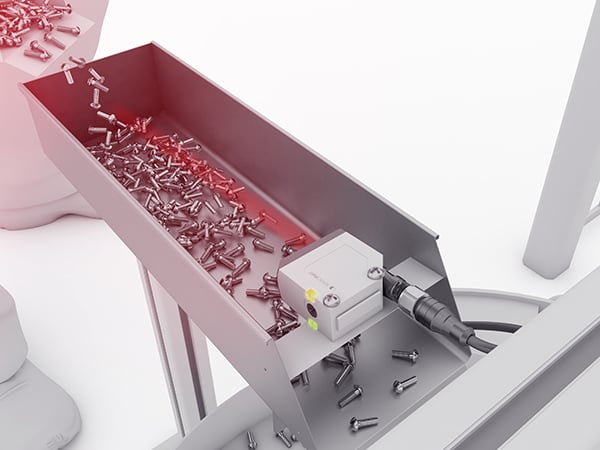
THE CHALLENGE
A large number of screws are processed during the assembly of a battery pack.
To avoid interruption, it is important to be notified when the screws need to be replenished. The sensor must not interfere with the handling area, and it is complicated further by the stainless steel body of the storage bin being reflective and the refill flap being transparent.
THE SOLUTION
This is a good example of an instance where a BlueLight sensor can perform the same task as a red light sensor in detecting when a predetermined level of screws has been reached. Both systems are equally effective at solving this application.
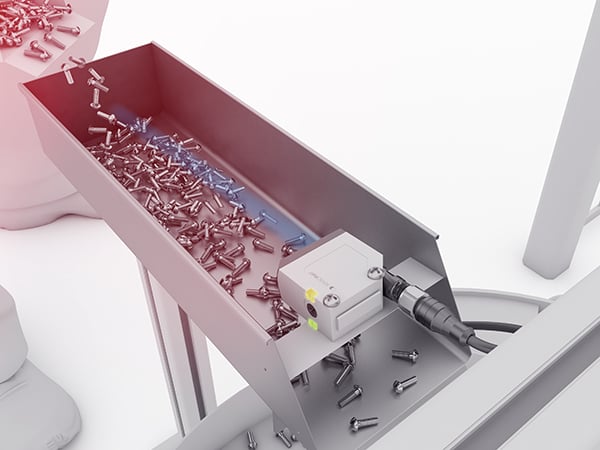
SCENARIO B: DETECTION OF PLATES ON THE CONVEYOR BELT
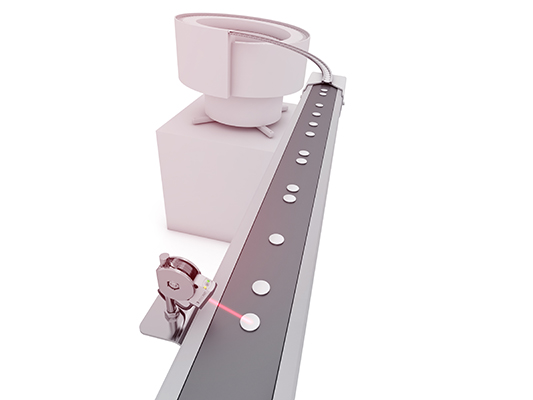
THE CHALLENGE
Another task in industrial automation is the detection of plates with the help of optical sensors. The surface properties of some plates can present a problem as it can be very bright white and also very reflective. Further complicated by the constant movement of the conveyor belt.
THE SOLUTION
The bright white and reflective plates can be reliably detected using either red light sensors or BlueLight sensors. Both the red and blue emitting LEDs enable high process stability, even with these challenging bright, white surfaces.
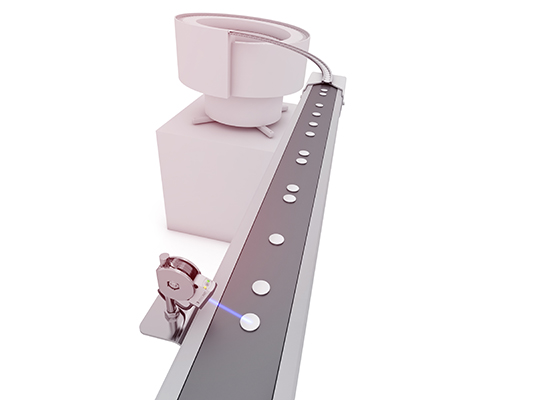
You want to know whether blue light or red light sensors are the right choice for your application?
Then download our brochure to find out which sensor is the ideal choice.
SCENARIO C: DETECTION OF PLATES IN THE ROBOT GRIPPER
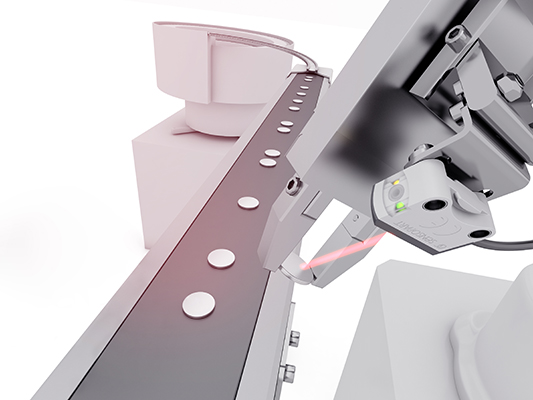
THE CHALLENGE
A related task to scenario B above is the industrial automation needed to detect and grip plates with the help of a robot and optical sensor. The sensors need to check the presence of the plates in the robot gripper, which is made more difficult by the very bright white and shiny surface of the plates.
THE SOLUTION
The red light sensors and BlueLight sensors are able to reliably detect the bright plates in the robot gripper. Again, both the red and blue emitting LEDs enable high process stability, even when space is tight and the sensor is mounted on the robot gripper.
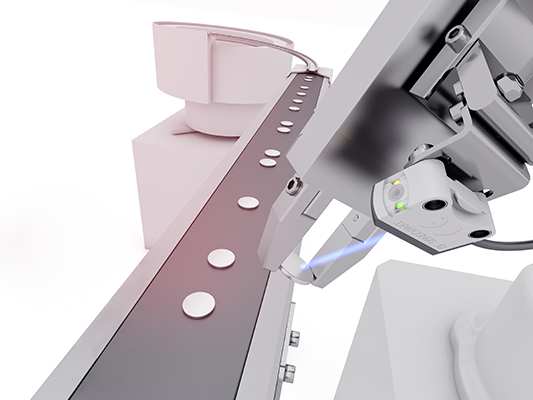
SUMMARY
While red light sensors are the conventional choice, BlueLight sensors are true all-rounders and are fast becoming the industry standard. Whether for applications
or objects with demanding surfaces, they detect reliably and with process stability. For each application, the particular merits of red light and BlueLight sensors
must be considered individually.