Target Mark 3D
High-accuracy 3D robotics
The "Target Mark 3D" function of the VISOR® Robotic vision sensor from SensoPart simplifies the spatial orientation of handling and assembly robots - with just a few mouse clicks and minimal programming effort in the robot controller.

An important factor for efficient work is quick orientation at the workplace - this applies to both people and machines.
People can still find the screwdriver even if it is at the other end of the table. This is where it becomes problematic for robotic solutions. Even small shifts in the working position, for example due to the inaccurate delivery of load carriers or inaccurate docking of mobile robots at the workstation, make the process unstable. Instead of carrying out time-consuming reprogramming of the robot in such cases, these dynamics can be corrected simply by means of a target mark.

All that is needed is to place a target mark and select the "Target Mark 3D" detector in the configuration software of the VISOR® Robotic.
The position of the target mark only has to be referred to in the robot control during the initial setup. After that, the vision sensor is able to extract the 3D information from the image and pass on any displacement to the robot.

Each target mark is unique - several target marks can also be placed within a production environment in order to automate different processes.
For this purpose, a freely selectable name can be assigned in the detector for each mark (e.g. "Station 1").

The targets themselves are made of a robust, highly reflective material, so that correct detection is always guaranteed even in difficult lighting conditions.
Another advantage of SensoPart's target marker system: unlike proprietary solutions from some robot manufacturers, it can be used across platforms, which also enables retrofitting. Above all, the temporary use of mobile robotics stations can be made extremely efficient and cost-effective with Target Mark 3D. The technology is available for all product variants of the VISOR® Robotic.
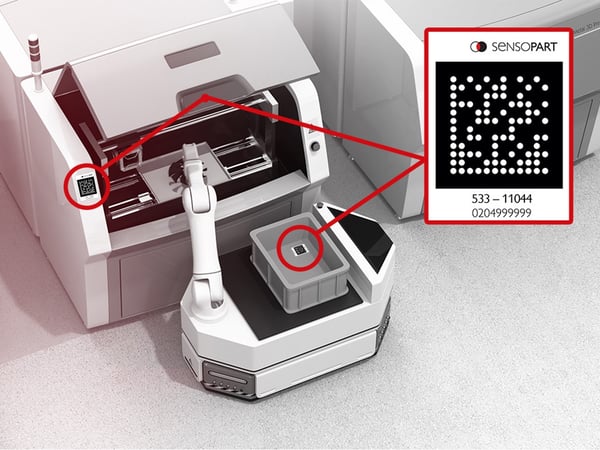
on the workstation.
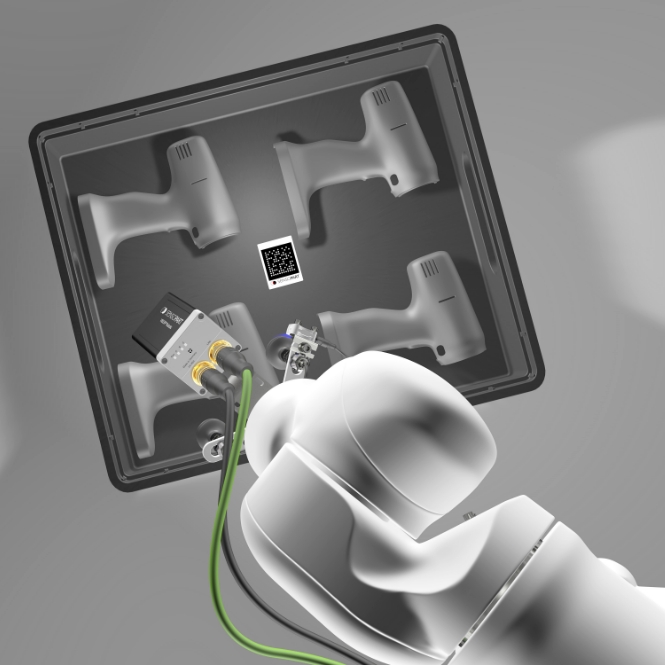
Material feed from a carrier
Components for the production process are often supplied in load carriers. The challenge is to position the load carriers as precisely as possible, as this is imperative for a stable, robot-aided handling process.
The VISOR® Robotic and Target Mark technology determine any inaccuracies in the position of the load carrier. Its position is then recalculated in the VISOR® and transferred to the robot in corrected form. This is achieved with the help of a special target mark fitted on the load carrier, whose 3D position is reliably and efficiently detected throughout the procedure. The robot uses this information to correct the pick-up points of all the components in the load carrier, thereby maintaining a stable process.
Benefits for the user:
- Considerable cost advantages due to the use of universal load carriers for all product versions,
instead of special custom-made designs - Greater flexibility due to the elimination of mechanical elements for immobilising and aligning parts
- High process reliability even when parts are inaccurately fed
Mobile workstations
The flexible use of mobile robots is an attractive solution for machine tending processes. Yet this flexibility can cause robot positions to be comparatively imprecise. The success of this solution – whether or not the robot can carry out the tending process correctly – depends primarily on the precision of the robot's movements in relation to the machine.
Target Mark 3D technology solves this problem by placing a coded mark on the machine. The robot program is then written and references the mark. If the robot is repositioned by the user, for example on a mobile platform, Target Mark technology detects which machine is to be tended and the size of the offset to the machine and then corrects the robot program accordingly.
The benefits for the user:
- The combination of mobile robots and the option of automatic selection of tending programs makes the use of robotics a viable solution even for small companies
- Significant cost benefits, reduced maintenance and more sustainable and ecological operation by deploying individual robots for multiple tasks on different machines
- The unique simplicity of a one-click setup allows processes to be automated without expert knowledge
- High process reliability even when robots are inaccurately positioned
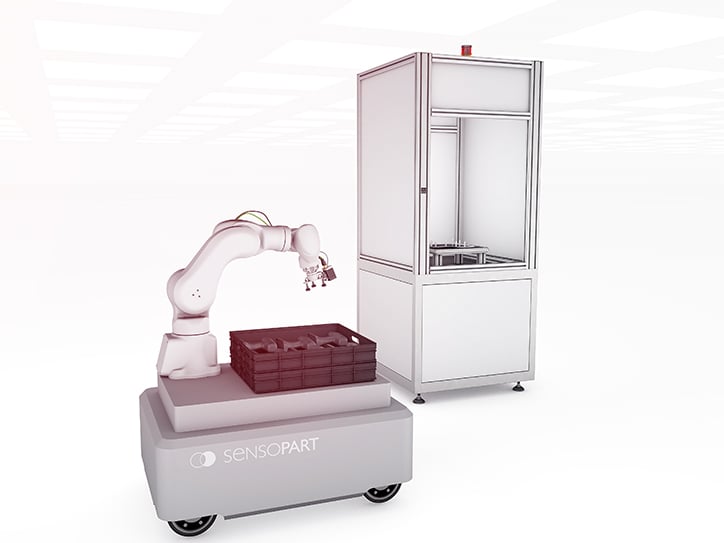
Get the brochure
Find out how you can automate smarter with high-accuracy robotics
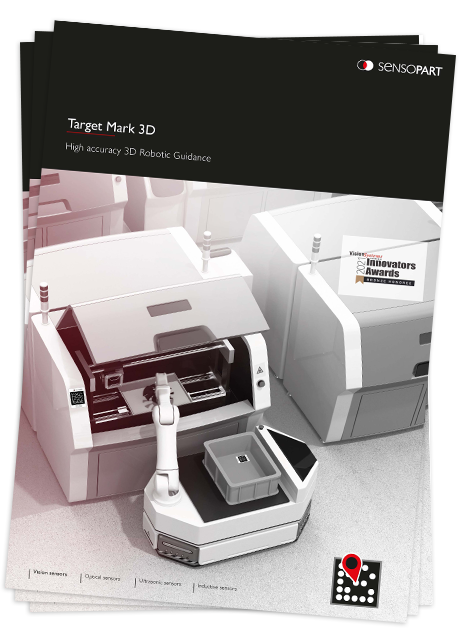