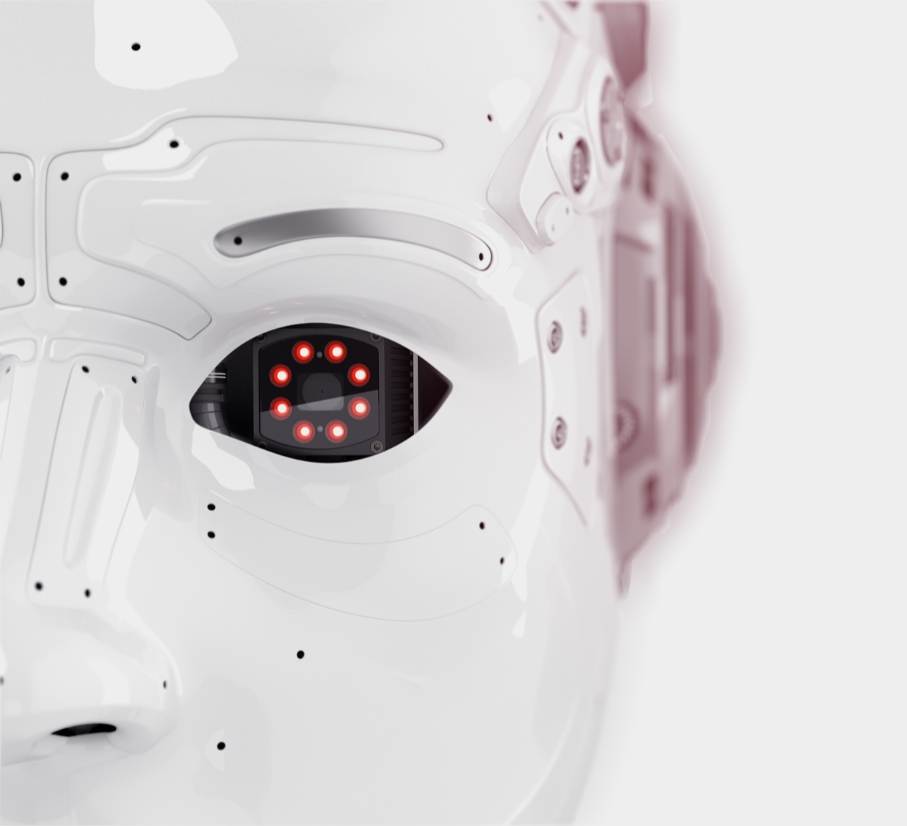
Ready for a revolution in industrial production? Because that’s exactly what vision-guided robotics represents! The use of cameras and machine vision systems enables robots to identify objects and handle them precisely.
In many cases, cameras have replaced complex and expensive-to-maintain mechanical guides. The cameras serve as the eyes of the robot, providing important information to the control unit. So it can approach the target position with pinpoint accuracy.
The adaptability of robots and the ease of implementing vision technologies allow companies to respond more flexibly to customer requests and make production more efficient. Although the integration of vision sensors on the gripper may initially make the robot more complex and expensive, the overall costs decrease due to the elimination of expensive expert systems that were previously needed to design and set up robotic cells. So vision-guided robotics offers a more cost-effective and efficient alternative to traditional methods.
It’s no wonder that vision-guided robotics is becoming popular. The technology enables greater efficiency, quality, and profitability in production. Be ready to be part of the future of production and discover the incredible power of camera-guided robotics!
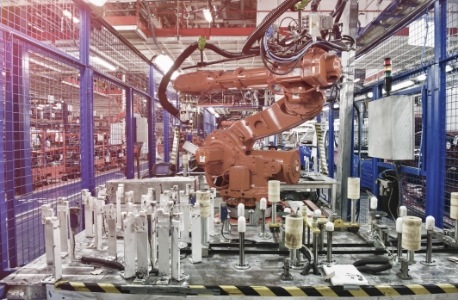
Articulated arm robots
These robots are used in the mechanical engineering and automotive industries to execute complex motion sequences.
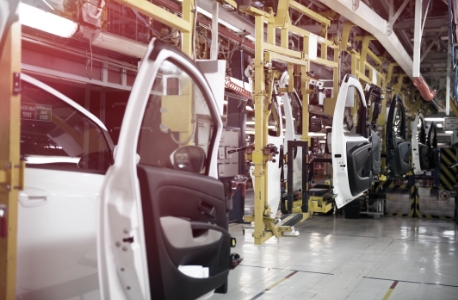
Gantry robots
These robots are large and robust, so they can transport large loads over long distances. They are often used in logistics
and packaging.
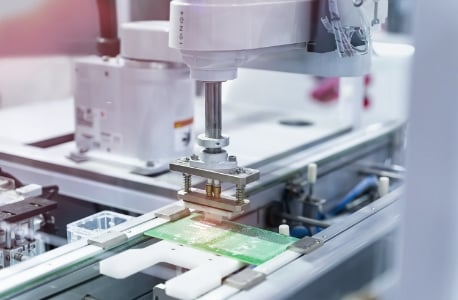
SCARA robots
Short for Selective Compliance Assembly Robot Arm, these industrial robots have a parallel articulated designed for fast and precise assembly and manufacturing processes.
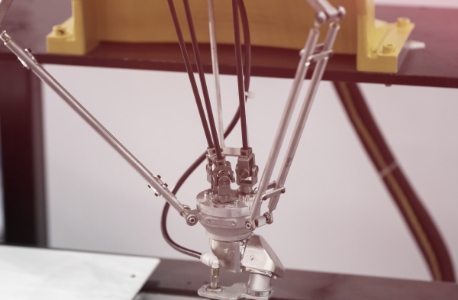
Delta robots
Light and fast robots that are particularly suitable for packaging tasks due to their flexibility and speed. They have a triangular structure and can move quickly and precisely in a limited
work area.
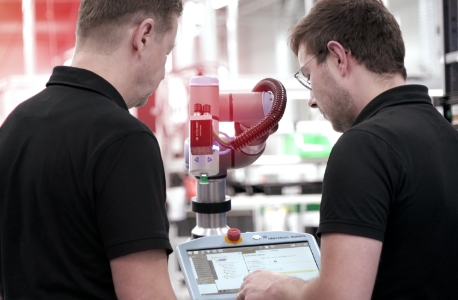
Cobots
These collaborative robots work with humans to assist with complex tasks that cannot be fully automated. They are used in many areas, including assembly, handling and inspection.
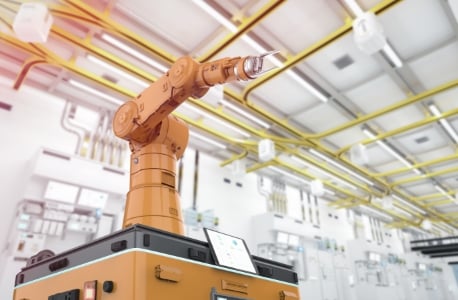
Mobile robots
These autonomous mobile robots (AMRs), move around on wheels or tracks. They can be used in a variety of environments and tasks, from plant inspection and maintenance to picking and delivering goods. You can also mount a second robot on an AMR, so it doesn’t need a separate station and can be equally mobile.
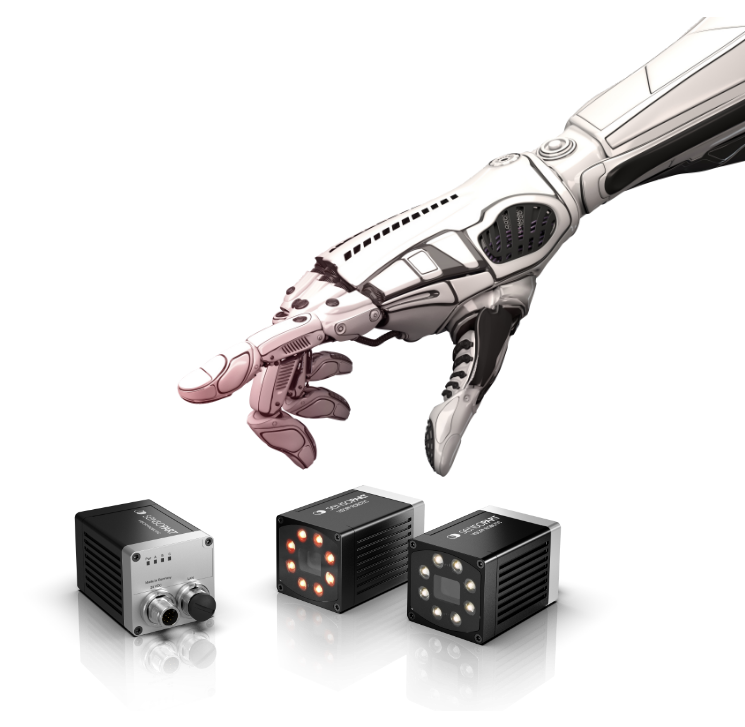
Vision-guided robotic sensors play a crucial role in modern robotics. They allow robots to recognise defined objects or scenes in their environment. So they can respond and carry out actions.
A vision sensor captures visual information from the robot’s environment and evaluates it. For instance, it might detect particular objects or determine their position. The sensor then translates this information into commands and signals the robot can process. In this way, the robot can adapt its actions to the environment and perform precise tasks.
Traditional robotic systems often work with fixed coordinates and predefined movements. However, this approach has its limitations when it comes to complex or variable tasks. In such scenarios, traditional robots reach their limits as they have difficulty adapting to new environments
or requirements.
To process images, cameras use algorithms and techniques such as edge and contour detection, feature extraction and pattern recognition. Object recognition is a key component here, helping robots to identify, track and manipulate specific objects in their environment.
The interaction of cameras and robots is essential for robots to work efficiently with
their environment.
Key industries for vision-guided robotics
Vision-guided robotics is a fascinating technology that is used in various fields such as assembly, material handling, packaging, joining and logistics. Robots can use cameras and sensors to see and understand their environment, enabling greater precision and efficiency than manual methods, resulting in higher profitability and competitiveness. The future of vision-guided robotic sensors looks promising as it is used in more and more areas, helping to optimise companies’ production.
Automotive
Robots enable precise positioning and faster joining of body parts. They can also perform leak tests, insert battery modules, screw housings, assemble electrical plugs, and more.
Assembly
Robots can piece together components, such as electronic components on printed circuit boards. They can detect the exact position and orientation of parts, so they can work with high accuracy
and high speed.
Material handling
Robots can recognise the size and shape of materials such as metal or plastic, as well as manipulate them. So they can sort, stack, or place materials, boosting the throughput of production processes.
Packaging
Robots can pack products by recognising the size and shape of the products and placing them in the correct packaging or sealing boxes. They can also handle product changeovers quickly and easily, speeding up throughput.
Joining
Thanks to their precision and speed, you can use robots in many joining and connecting processes. This includes welding, screwing, soldering, gluing or riveting components.
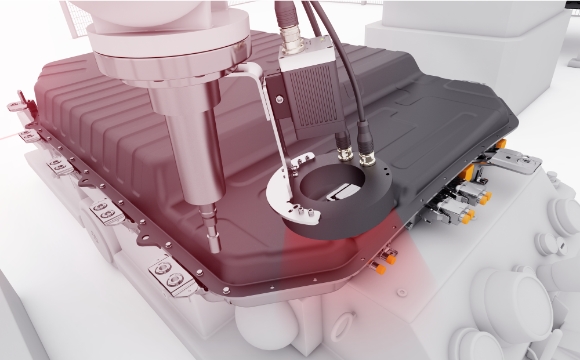
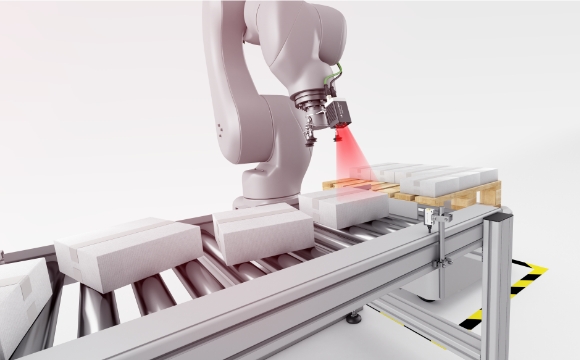
Logistics
Robots can sort packages on conveyor belts or in warehouses. And because cameras and sensors allow them to react in real time, they can work well even in a hectic workplace. So you can ensure goods ships on time, every time.
Overcoming industry challenges with cutting-edge technology
Modern manufacturers face lots of challenges. Labour costs continue to rise and the growing demand for high-quality products leaves little room for error. Workplace accidents and health risks not only affect employees but can also lead to high liability costs and loss of profits. Governments and consumers are increasingly focusing on environmentally-friendly technologies, which means that companies need to make their production processes more sustainable. Lacking the flexibility to adapt to changing workplaces, traditional robots can’t help overcome these industry challenges. But vision-guided robotics can.
Robots can help fill staff shortages and relieve human employees of repetitive tasks, freeing them up to focus on more important jobs. Robots can also help to increase the flexibility of production lines and improve the company’s responsiveness to market changes and new product requirements.
Traditional robot systems are often specialised for certain tasks and environments, with fixed coordinates and predefined movements. Adapting for new processes and environments requires a lot of time and money, so companies can’t respond quickly to market changes. This limits the flexibility of production lines and affect a company’s competitiveness.
Cycle times in current production are often longer than desirable. This leads to bottlenecks and delays in manufacturing. The high labour costs associated with using human workers are a drain on the company’s budget. At the same time, there is an increased safety risk as workers are exposed to dangerous or tiring tasks. Finally, integrating new technologies into existing production environments is often difficult and time-consuming.
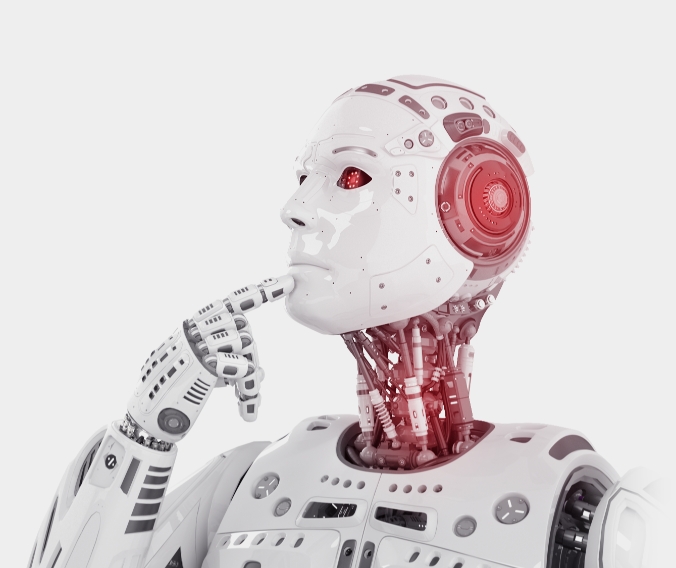
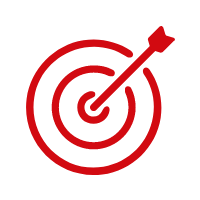
Accuracy
Unlike traditional robots, camera-based robots are dynamic and adaptable. They
work precisely and efficiently, even in changing environments.
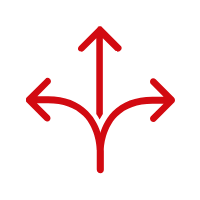
Flexibility
Image-guided robots can be easily reprogrammed and adapted to meet changing production requirements. So companies can react quickly to market changes and maintain their competitiveness.

Quality assurance
Robots can use cameras to inspect products and components, ensuring they meet the highest quality standards.
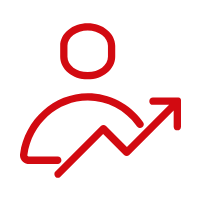
Cost and labour savings
Robots can carry out repetitive or hazardous tasks on behalf of human workers. This leads to a reduction in operating costs and increases competitiveness.
Camera resolution
One of the most important factors is the resolution of the camera. A higher resolution means a robot can recognise finer details and make more precise movements. However, processing a high-resolution image can need more computational effort, which can affect how quickly a robot can act.
Design and concept
Think about how the camera will be used. For instance, in end-of-arm tooling applications, the camera is mounted on the robot’s gripper arm. So the camera needs to be lightweight and compact, so as not to affect the weight of the gripper and to ensure precise positioning of the camera.
Speed
The speed of the camera is also an important factor. A fast camera allows the robot to make faster decisions and perform its tasks faster. However, too much speed can also lead to more computational effort, which can affect the robot’s performance.
Camera type
The type of camera can also have a big impact on the performance of the robot. There are different types of cameras that should be selected depending on the requirements of the application. For example, a colour camera can help identify objects, while a 3D camera can be useful for measuring distances and creating three-dimensional models of objects.
Calibration
Precise calibration of sensors and cameras is critical to the accuracy of robot guidance. Schedule regular calibration and maintenance.
Software
Ensure compatibility of sensors and cameras with the robot control software and algorithms used to ensure seamless integration and efficient operation.
Environmental conditions
Think about the temperature, dust, humidity, and vibration of your workplace when selecting sensors and cameras. Make sure they are suitable for the given conditions.
Lighting
Appropriate lighting is critical to the quality of image capture. Consider the use of LED ring lights, spotlights or external light sources to ensure even illumination and avoid shadows or reflections.
Field of view
The field of view of the camera and the working distance to the object should be considered in the planning phase to ensure adequate image coverage and sufficient space for the robot movements.
Selecting the appropriate camera for a vision-guided robot system can be a complex and important decision that directly affects the performance of the robot and the quality of the results. A vision expert can help select the appropriate camera by considering all relevant factors such as resolution, sensitivity, speed, type of camera, calibration, compatibility, environmental conditions, lighting, and field of view. Thorough planning in the initial stages helps ensure that robot vision runs smoothly and delivers optimal results.
Find the right camera for you
Take our quick questionnaire to find out how you can best embrace vision-guided robotics
and optimize your production.
Imagine a robot that interacts with its environment. It can identify components at lightning speed. Recognise exactly how to position and assemble them. The secret behind this remarkable capability lies in the sophisticated cameras and vision software that equip the robot with eyes to ‘see’ and react to its environment.
But that is just the beginning. A simple adjustment in the camera software allows robots to react quickly and flexibly. It can instantly embrace changing production requirements. This enormous potential for rapid adaptability is already revolutionising production. Making even more efficient and versatile manufacturing possible.
Take control of quality control
In the world of production, quality is the be-all and end-all. And here too cameras play a crucial role. They are the watchful eyes of the robots, detecting defects and irregularities. While ensuring that only flawless products leave the production line. This precision in quality control not only saves costs, but also contributes to the reputation and success of companies.
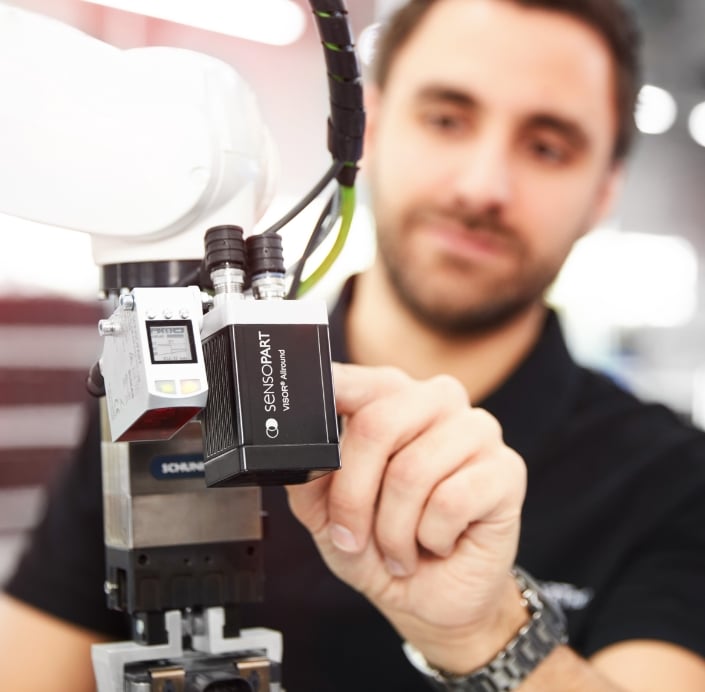
The introduction of automated systems and robots in manufacturing offers companies the opportunity to increase their productivity and efficiency.
However, many companies have concerns about the reliability of robots and their impact on production. In particular, high initial costs for robotic systems often cannot justify the expense for smaller quantities, and finding and programming the right system often requires expertise, which is hampered by the shortage of skilled workers.
Traditional robot systems have the disadvantage that they are specialised for certain tasks and environments and can only be adapted to new processes and environments to a limited extent, which limits the flexibility of production lines. With image-guided robots, there is a lot to think about. Is the vision system accurate enough for my robot to grip precisely? Can it counteract for the ambient light? Will the added processing time make my robot slower?
To meet these challenges, we’ve developed a solution: the SensoPart VISOR® Robotic sensor. This vision sensor can be directly connected to leading robot systems. Specific interface modules make programming and integration easier and enable the automation of tasks that previously seemed too complex or expensive.
“The VISOR® Robotic offers a wide range of application possibilities”,
says our vision expert, Lothar Stöcks, so it can take your production to
the next level. Read the full interview.
Precision and efficiency:
The diverse applications of the VISOR® Robotic
The VISOR® Robotic solves a wide range of applications in various industries.
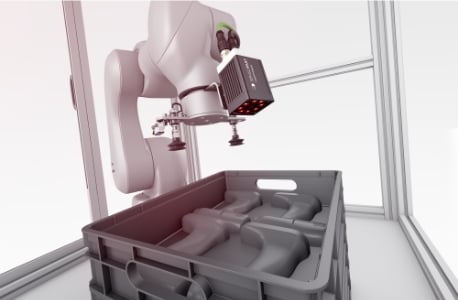
Safe material feed
With the VISOR® Robotic, components are reliably located and gripped - when parts are fed in a universal load carrier or via hopper feed.
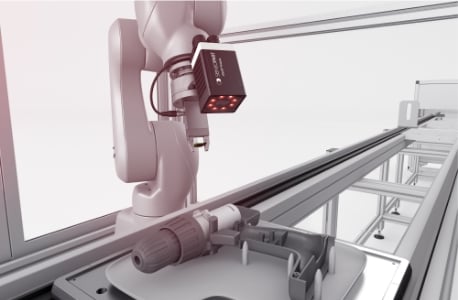
Precise machining of components
In robot-guided applications such as the placement of screws, the VISOR® Robotic effortlessly detects the component position, thus enabling the correction of the positional offset and increasing the quality of production.
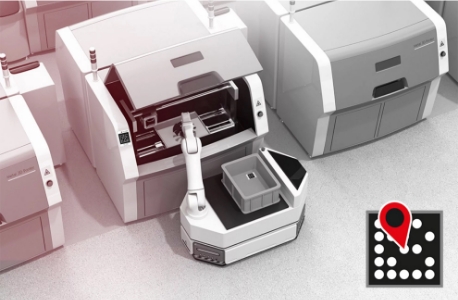
Precision for mobile workstations
The VISOR® Robotic ensures safe and efficient use of mobile robots and allows the worker maximum freedom of movement. Thus, mobile robots can precisely calibrate themselves at the workstation and mechanically connect there, e.g. via
a connector.
Realise a wide range of 2D and 3D applications
The seamless integration of vision sensor and robot opens up a wide range of robot-guided application possibilities in 2D and 3D environments. Pick-and-place applications can be effectively automated using vision-guided robotics. Examples include parts feeding and assembly in the automotive and supplier industry as well as the placement of circuit boards in electronics manufacturing. Due to the environmental information provided by the vision sensor, deviations in the position of components can be detected and immediately corrected by the robot.
Furthermore, the boundaries between 2D and 3D applications are fluid. For example, if the robot needs additional height information to pick up multi-layer sheet stacks, a 3D vision system is not necessarily required for this.
The Target Mark 3D feature in VISOR® Robotic allows the robot to read and respond to highly accurate 3D information and position data, enabling a simple, intelligent, mobile and autonomous workspace. The target mark position is only referenced once during initial camera setup and can then be easily relearned by any VISOR® Robotic camera, maximising time, efficiency, and accuracy.
Target Mark 3D accurately detects even the smallest deviations in working position and seamlessly corrects them without the need for reprogramming.
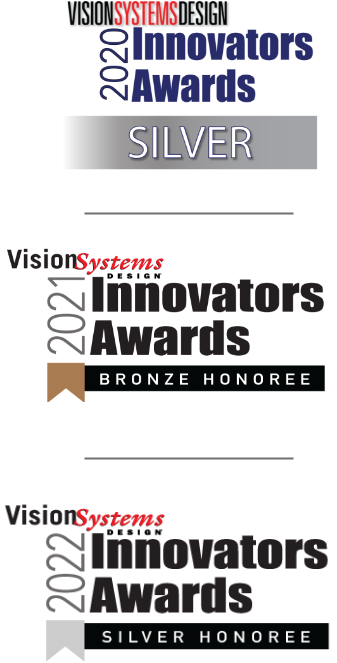
Discover the smart machine vision of the VISOR® Robotic
The quality of the machine vision processing is decisive for the precision of the robot. The VISOR® Robotic has a variety of image evaluation algorithms, such as the contour detector or BLOB detector, which enable an optimal detection rate depending on the type of part and application.
The contour detector detects the characteristic part shape based on the part edges.
For irregularly shaped objects, the BLOB detector, compares the foreground and background– like a loaf of bread on a conveyor belt, for example.
Especially for the cooperation with the robot, the VISOR® Robotic offers special functions that facilitate the automated gripping of the detected parts. The gripper clearance check checks whether the part has sufficient clearance to neighbouring parts when it is fed loosely. A predefined gripper offset informs the robot that the part should not be gripped in the centre but, for example, on a lateral gripper. With these intelligent functions, the VISOR® Robotic enables precise and efficient automation.
Award-winning performance
The VISOR® Robotic has already received three outstanding ratings and awards from trade journals. In 2021, the vision sensor was awarded the Handling Award in the Robotics category by INDUSTRIAL Production magazine for its unique Target Mark 3D technology. It also received an outstanding rating for Vision System Design’s Innovators Awards Program in 2020 and 2021 and 2022.
High resolution for variable image sections
The VISOR® Robotic packs a powerful camera with up to five–megapixel resolution, so you detect even the finest details over a great distance. It also three fields of view, so you can customise the vision sensor to best meet your needs.
The 5-megapixel version (VISOR® Robotic V50) extends the sensor’s field of view several times over. With a resolution of 2560 x 1936 pixels, the sensor achieves an image quality that is normally only available with more expensive and technically complex machine vision processing systems.
The VISOR® Robotic has eight high-power LEDs that ensure optimal internal and external illumination. This reduces the risk of extraneous light and ensures accurate and precise image capture.
It has an integrated aiming laser (laser class 1) and motorised focus adjustment. Making it easy to mount and align of the vision sensor.
You can also stay one step ahead. We continuously update the device with new and improved machine vision processing capabilities.
This all means VISOR® Robotic achieves a high evaluation rate without affecting the cycle time of the robot. So your robot can work precisely and reliably.
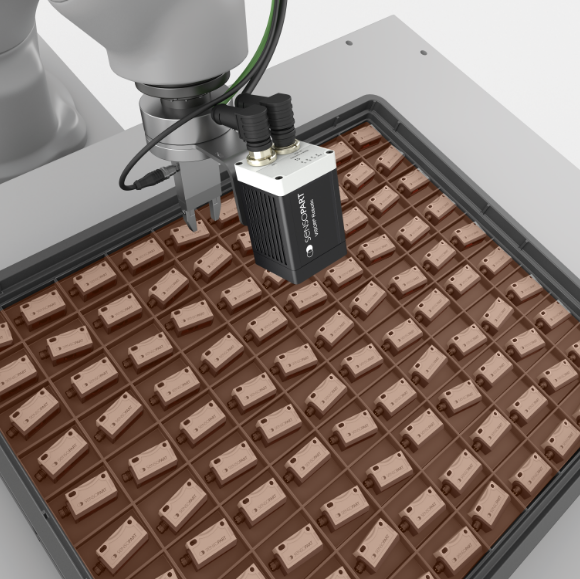
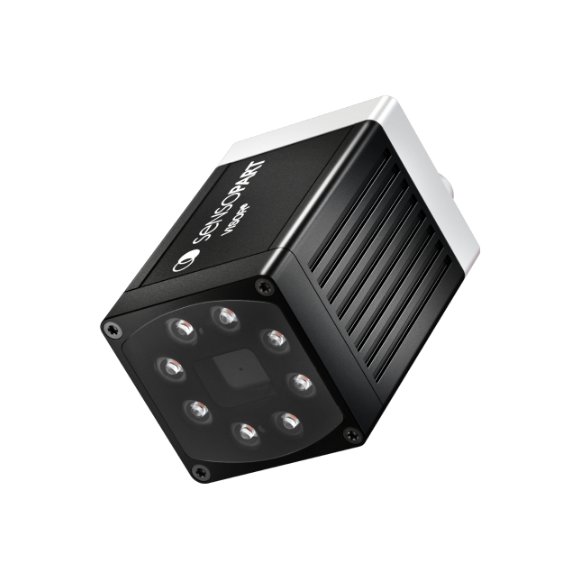
Compact, robust and versatile design
The VISOR® Robotic is versatile and, thanks to its compact, robust and lightweight design, is equally suitable for stationary or moving use on the robot gripper.
The housing is designed to withstand the demands of industry and at the same time can be used flexibly in various applications.
The low weight and compact size make the VISOR® Robotic particularly suitable for use on robot arms or grippers. Due to its robust housing, the VISOR® Robotic is also suitable for use in adverse conditions, such as dusty or humid environments.
Easy integration with a choice of connectivity options
The VISOR® Robotic is equipped with a wide range of connectivity options to enable seamless integration into existing plants.
These include interface protocols such as sFTP, TCP/IP, EtherNet/IP and Profinet Conformance Class B, which ensure easy connection to PLC or PC systems.
In addition, manufacturer-specific robot apps and function modules for robot systems from leading manufacturers such as ABB, KUKA, Stäubli and Universal Robots offer the possibility of closing the gap between machine vision processing and robot control. This eliminates the need for manual programming of the communication interface in the robot’s control software.
The intuitive teach-in function enables the robot to be quickly set up for a specific task by setting up the details of image acquisition and evaluation step by step in the vision sensor’s configuration software. These comprehensive integration options not only save time, but also minimise
application risk.
Thanks to the matching robot apps, simple applications can be solved quickly and effectively without requiring any knowledge of robot programming. This means that even inexperienced users can use the VISOR® Robotic quickly and effectively, resulting in significant time and cost savings.
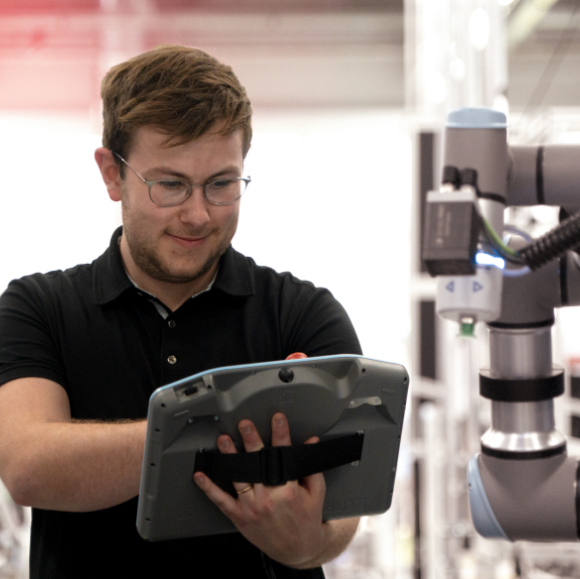
Works with leading robot manufacturers
We always provide easy-to-understand libraries for all the major robot brands, which you can customer to your needs
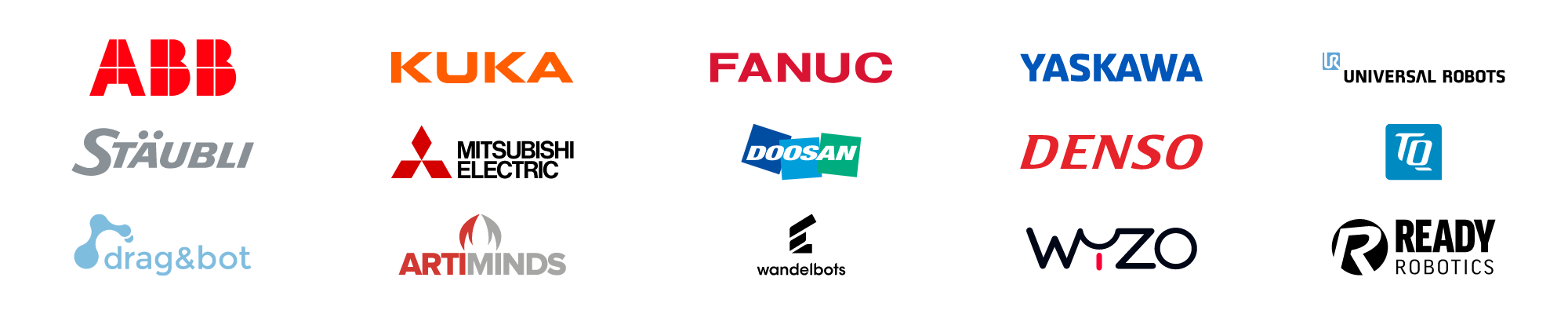
Precise motion control made easy
Get precise position detection and motion control with a choice of robot calibration methods. They all enable a simple transformation of image coordinates into robot coordinates – no programming needed!
Four methods are available, including hand-eye calibration and base-eye calibration, which are an effective way to calibrate sensors on the robot arm. Calibration with a SensoPart calibration plate is suitable for automated part feeding using vibratory feeders, for example.
With the help of the robot calibration function, you can carry out simple applications very quickly and effectively without requiring any knowledge of robot programming.
A one-time calibration via a calibration plate is also available as an accessory.
Explore the benefits of VISOR® Robotic in more detail
Unlock the hidden potential within your operations.
Our skilled sensor experts understand your challenges and provide tailor-made solutions.
With their in-depth knowledge and experience, they will empower you to take your production to new heights