Interview with a robotics expert
Join us for an insightful interview with Lothar Stöcks, our robotics expert and Sales Manager in Germany at SensoPart, as we explore the world of VISOR® Robotic and image-guided robotics. Discover the numerous advantages, versatile applications, and seamless cooperation between vision sensors and robots.
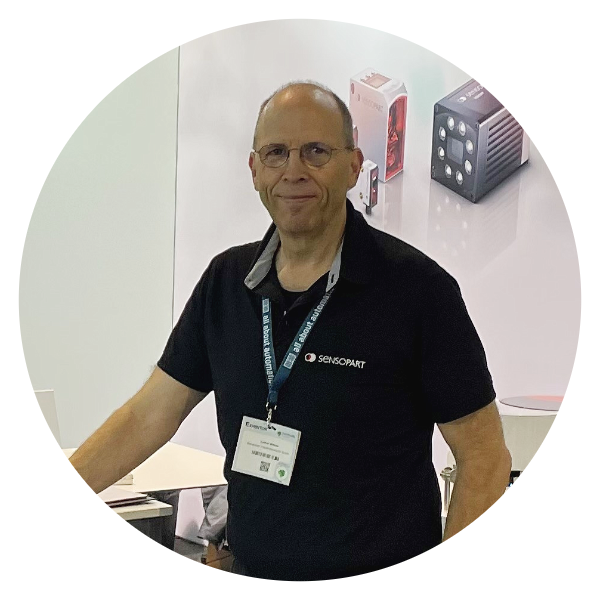
Sales Manager at SensoPart Germany
Why was the VISOR® Robotic developed?
Integrating vision systems into robot controllers is often a challenge. The VISOR® Robotic was developed to meet our customers' needs for a simple and user-friendly solution to this requirement. With the VISOR® Robotic, the unity of "seeing and grasping" with robot and camera is made possible in broad application areas, also known as "RoboVision" or "vision-guided robotics".
What are the advantages of VISOR® Robotic for users and system integrators?
The VISOR® Robotic offers numerous advantages for users and system integrators. One of the most important advantages is the simplified and standardised integration or connection of the VISOR® functionality into the robot controller and the HMI of the robot operating system. In addition, the convenient calibration functions enable the "pixel world" of the VISOR® Robotic to work directly in the robot coordinate system. These functions make the setup and operation of robotic applications easier and more efficient, especially for applications such as pick-and-place, assembly, gluing or screwing.
Which application areas are particularly well suited for the use of the VISOR® Robotic?
The VISOR® Robotic offers a wide range of application possibilities and is an optimal solution especially in pick & place applications as well as in presence checking. In pick & place tasks, objects can be detected, identified and positioned quickly and precisely with the help of the VISOR® Robotic. Even if the component position varies, the VISOR® Robotic enables the correction of the position offset and increases the quality of production. The vision sensor thus ensures a stable process even when the position of the components in the feeder varies. The VISOR® Robotic also offers high flexibility and precision in other areas. For example, welding processes or gluing tasks can also be supported with the help of the vision sensor.
How are the application areas of VISOR® Robotic distributed and which industries
use this technology?
The VISOR® Robotic has proven to be a reliable solution in various industries, including assembly, handling, packaging, logistics and plastic parts handling. It is successfully used in combination with robots for a wide range of applications. In particular, the automotive industry and the associated supplier sector like to use the vision sensor due to the high demand for efficient robotic processes. The VISOR® Robotic has already successfully contributed to the optimisation of automated production processes in many companies.
What is the advantage of the VISOR® Robotic software packages for specific robot manufacturers such as Universal Robots and KUKA?
The VISOR® Robotic software packages offer apps specifically tailored to the requirements of certain robot manufacturers such as KUKA and Universal Robots, which enable seamless integration of the vision sensor into the respective robot controllers. These apps offer easy set-up and configuration of the VISOR® Robotic, making it easier to program, commission and operate the robotic system. In addition, the apps are tailored to the specific functions and capabilities of the respective robots to ensure optimal performance and accuracy of the system. This allows users to benefit from increased efficiency and productivity when automating pick & place tasks and inspecting parts.
What is the benefit of the combination of robot and vision sensor?
The combination of robot and vision sensor brings numerous advantages to automated production.
By integrating vision systems, such as the VISOR® Robotic, parts can be reliably located and gripped regardless of their orientation, which makes a special alignment aid for each part shape superfluous.
Even if part shapes change frequently in a handling or assembly task, the sensor solution has an advantage over mechanical systems. With the use of a vision sensor, the development effort for teaching-in new parts shifts away from mechanical design to teaching-in new parts at the click of a mouse.
In addition, the sensor solution also enables problem-free gripping of inclined or offset parts.
A typical application is the robot-guided positioning of components, such as the precise placement of screws, the assembly of clips or the application of adhesives. By detecting the position of the component with the vision sensor, the position of the robot path can be precisely tracked or corrected.
The use of vision sensors not only reduces the development effort for teaching new parts, but also increases flexibility and efficiency in production.
Which new technologies/trends will make my assembly more flexible and efficient: Artificial intelligence, image processing, intelligent gripping technology or cobots?
The right combination of these technologies is crucial. In particular, the communication of image processing with grippers and robots is important in assembly processes. The issue of calibration is often underestimated. As early as 2017, SensoPart developed the VISOR® Robotic, a vision sensor for robotics that significantly simplifies the setup of applications with corresponding calibration options. With the user-friendly software and thanks to the wide range of functions, common 2D applications but also a position detection of objects in 3D coordinates can be solved with minimal effort in the robot control, regardless of the robot system used. With the innovative calibration options (hand-eye, base-eye, calibration plate, point pair list), the calibration of sensors on the robot arm or for stationary mounted sensors is also very simple and intuitive. With suitable interfaces and functions, the integration of such devices, e.g. in pick & place applications, assembly, gluing or even screwdriving processes, is much more efficient.
Which new technologies/trends will make my assembly more flexible and efficient: Artificial intelligence, image processing, intelligent gripping technology or cobots?
Collaborative robots, also called cobots, are being used more and more in production. They offer a solution for production processes where full automation is not possible or not desired. Cobots combine the strengths of humans (flexibility, judgement, creativity, experience, intuition and overview) with the advantages of robots (endurance, precision and strength). They work side by side with human workers without compromising worker safety. Cobots can also be used for simpler process steps, freeing up staff for more responsible and value-adding tasks. Thanks to the use of cobots in manufacturing, the barrier to entry for the use of robotics has been significantly lowered. Well-known manufacturers such as KUKA or Universal Robots offer a selection of cobots.
Why is a camera particularly important for cobots?
It needs more than just jointed arms and agile grippers. It must be able to see what it is doing. For this purpose, collaborative robots are combined with vision sensors. Without the sensor eye, a robot could only move to certain pre-programmed or calculated positions. As soon as a part was not exactly in the predefined position, it would be lost. The camera connected to the robot, on the other hand, recognises the object in question in the image and sends the real position to the robot so that it can grab it without any problems.