Applications that
VISOR® Robotic solves
In the data-driven world of industry 4.0, your smart factories need smarter robots. Vision-guided robotics, powered by camera systems and other sensors, can more accurately identify and handle objects to better meet your business needs, boosting your production processes. While vision also means they can adapt faster to change, helping you stay one step ahead of the competition.
Upgrade now with the VISOR® Robotic. It can handle complex applications with its award-winning Target Mark 3D technology. But it’s also easier to use, with a design that integrates seamlessly into your existing production line.
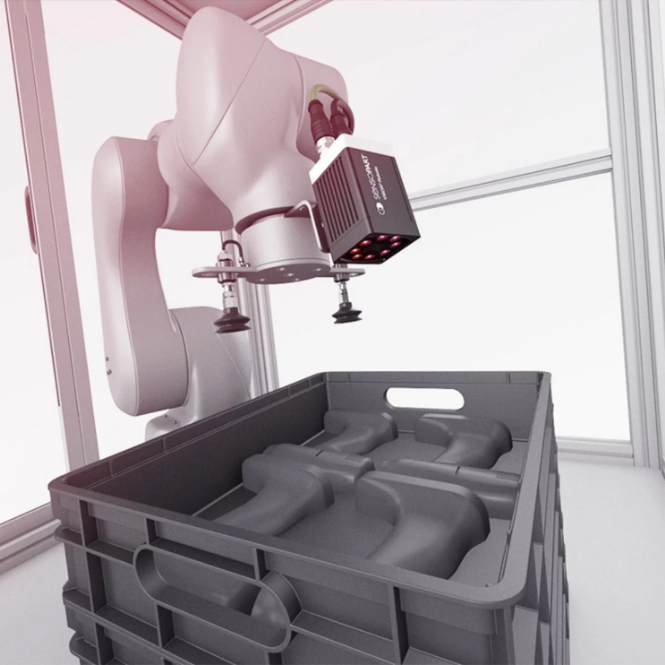
Reliable material feeding:
How VISOR® Robotic reduces costs and increases precision
Thanks to VISOR® Robotic, components that are fed in a universal tray or via a supply bin are reliably located and gripped. When loose components are supplied, the vision sensor not only checks their position but also inspects the free space around the gripper. The VISOR® determines both sets of information and sends them to the robot controller via one of the integrated standardised interfaces. The process is then managed based on the information received.
This results in a considerable cost advantage through the use of universal load carriers and the feed is very precise even without mechanical alignment. At the same time, commissioning is very simple thanks to the slim design and application-adapted functions in the vision sensor.
The benefits for you:
- Cost advantage due to use of universal tray
- Precise feeding, without mechanical alignment
- Easy installation of vision sensor through slimline design and functions tailored to the application
VISOR® Robotic:
The solution for precise processing of components in
robot-guided applications
During robot-guided applications, such as screw positioning, VISOR® Robotic effortlessly detects the pose of components; this allows the correction of any offset and improves the quality of production. Mechanical effort is reduced, and the production line is consequently more flexible. The Sensopart VISOR® Robotic concept enables direct communication between the VISOR® and the robot, and an additional instance can subsequently be omitted for
many applications.
By calculating the 3D approach position directly in VISOR®, the programming effort on the robot side is greatly reduced. The solution is therefore manufacturer-independent.
The benefits for you:
- Stable process despite varying positions of parts being fed
- Added flexibility with increasing number/diversity of variants
- Reduced programming due to calculation of 3D destination position for robot by VISOR® Robotic
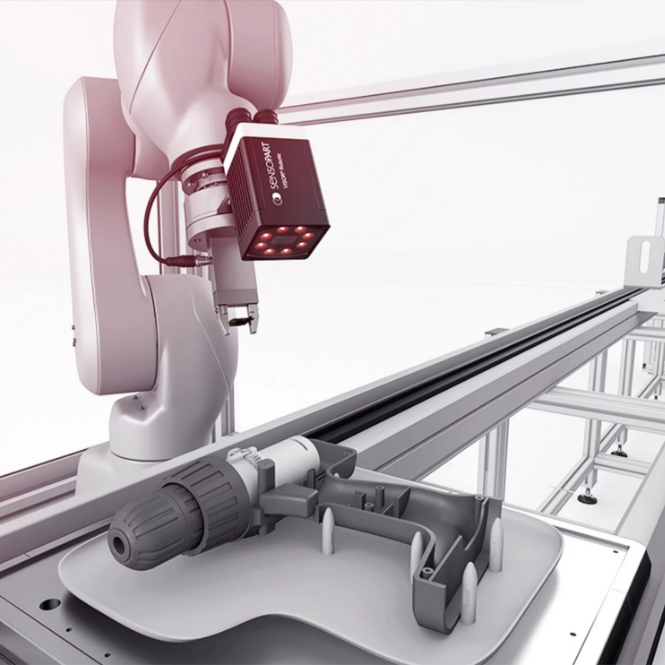
Mobile workstations:
Precision and safety through VISOR® Robotic
Use of mobile robots must be safe and efficient. To achieve this, the size of the safety zone must be rigorously defined, and also extremely reduced to offer the worker maximum freedom of movement. With the aid of Target Mark 3D technology, VISOR® Robotic sensor allows mobile robots to move with precision to the workstation and e.g. to connect themselves there mechanically via a plug.
High availability is guaranteed by taking over the safety areas of workstations, while at the same time fast processes can be achieved by compensating the 3D position offset by means of the 2D vision sensor with only one image acquisition
The benefits for you:
- High availability due to robots’ implementation of workstation safety zones
- Fast procedures due to compensation of 3D offset using 2D vision sensor with image capture
Get the white paper
Find out how you can automate smarter in e-mobility and battery pack assembly applications
Our easily integrated solutions can optimize your battery pack assembly. Our optical and vision sensors are reliable and easy to use in key applications at every stage. Find out more with our new white paper.
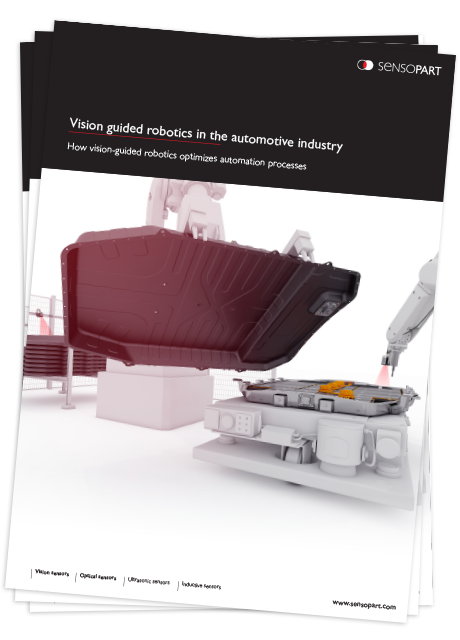
More VISOR® Robotic application examples
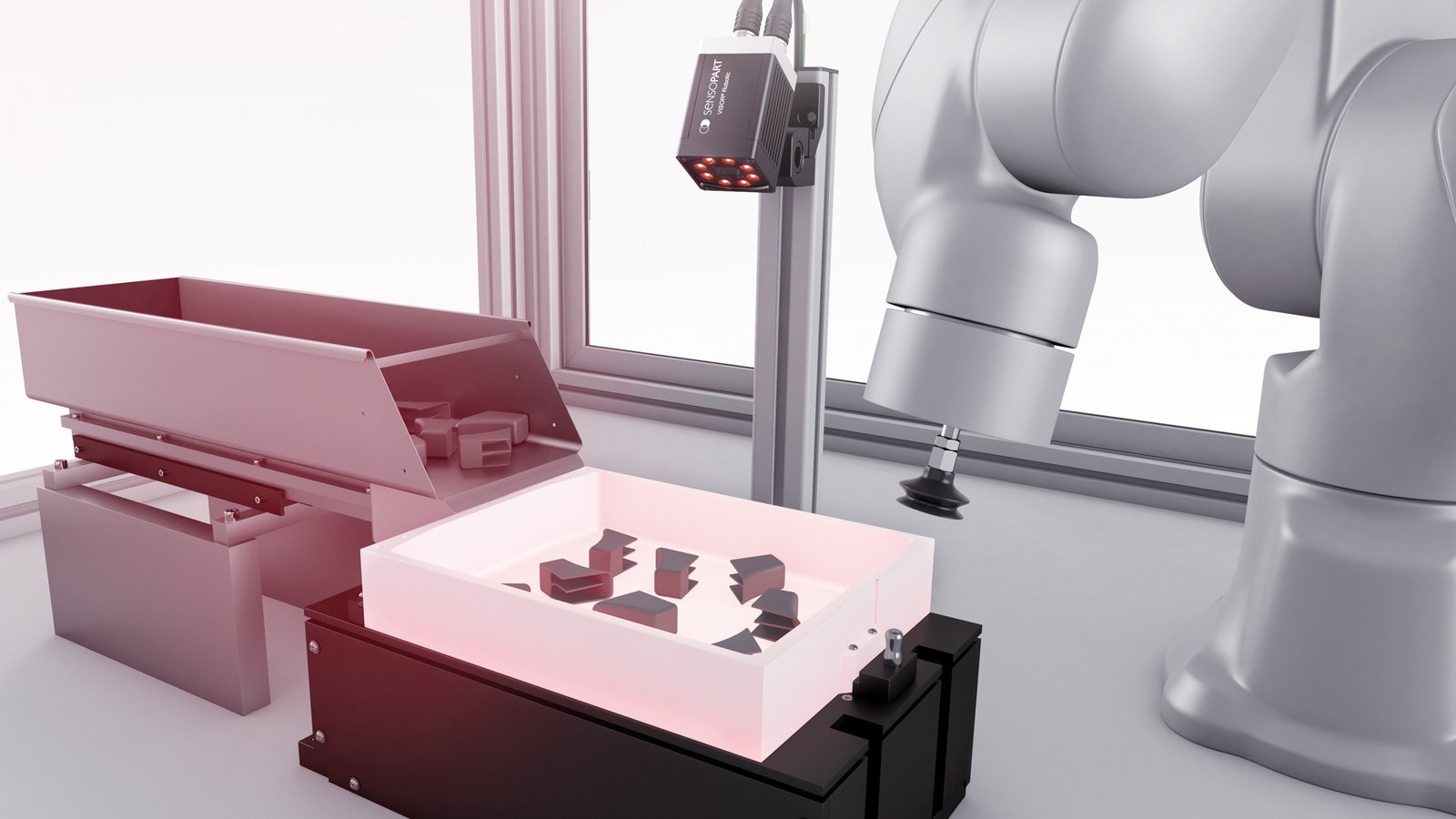
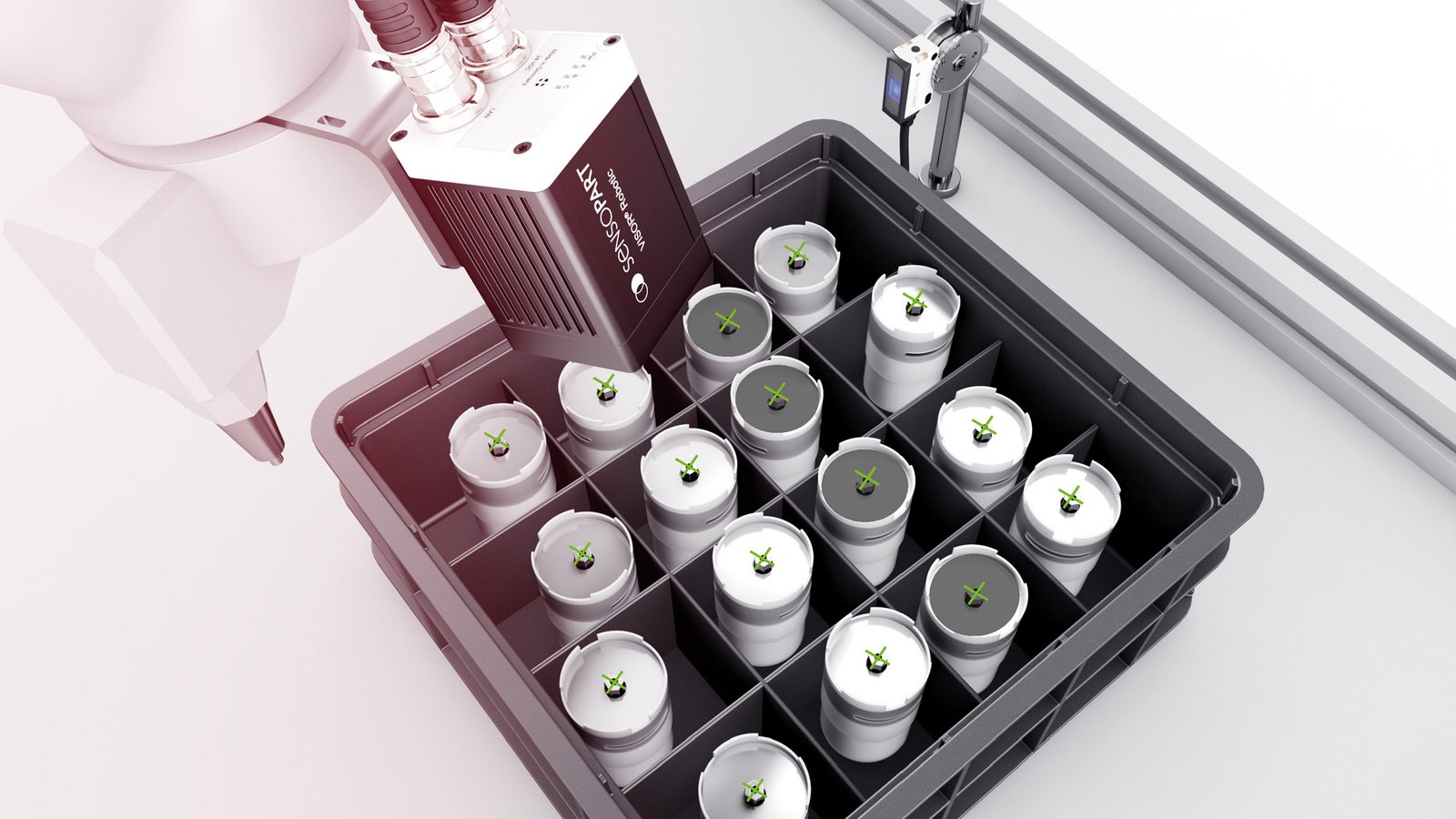
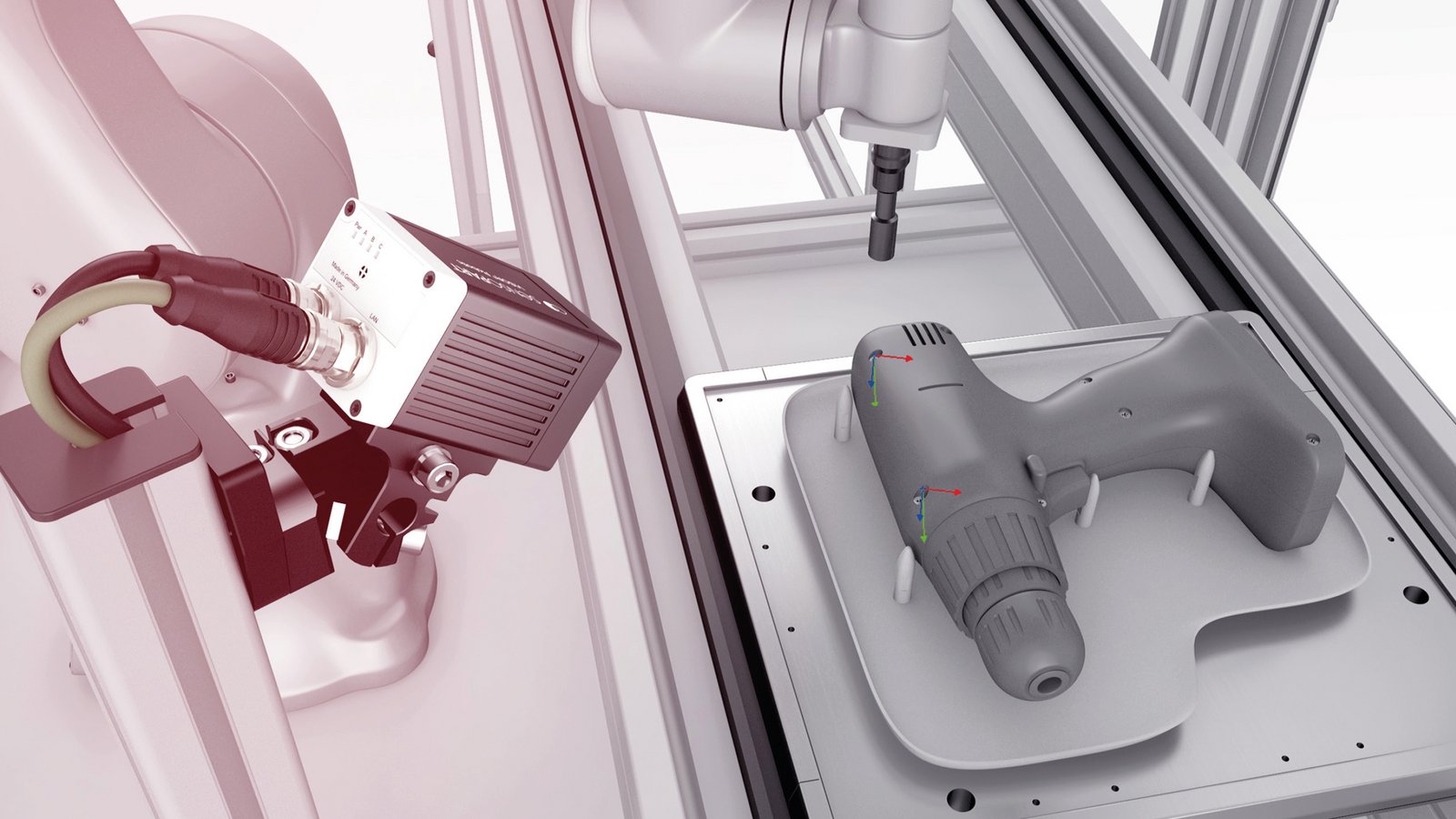
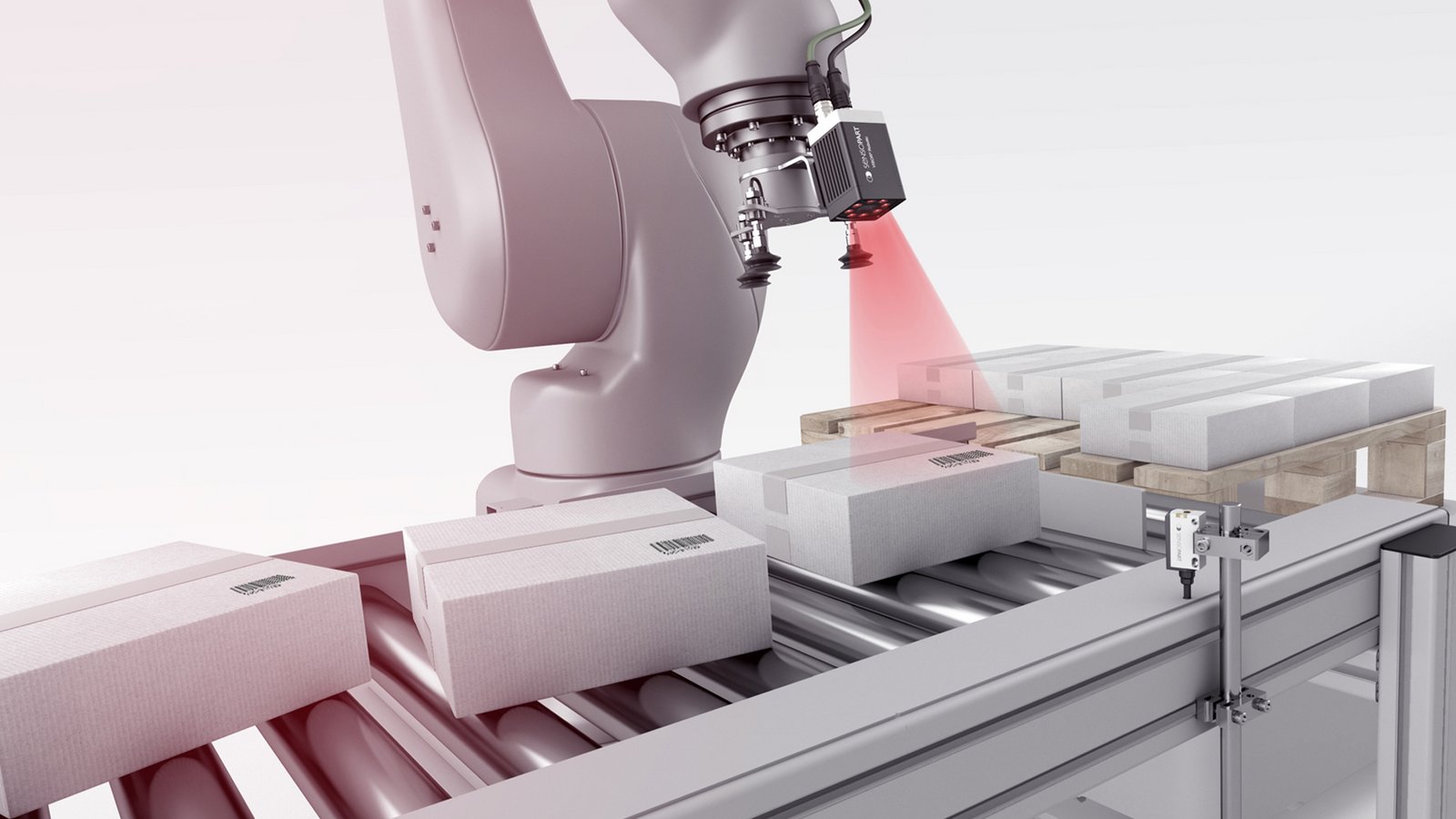
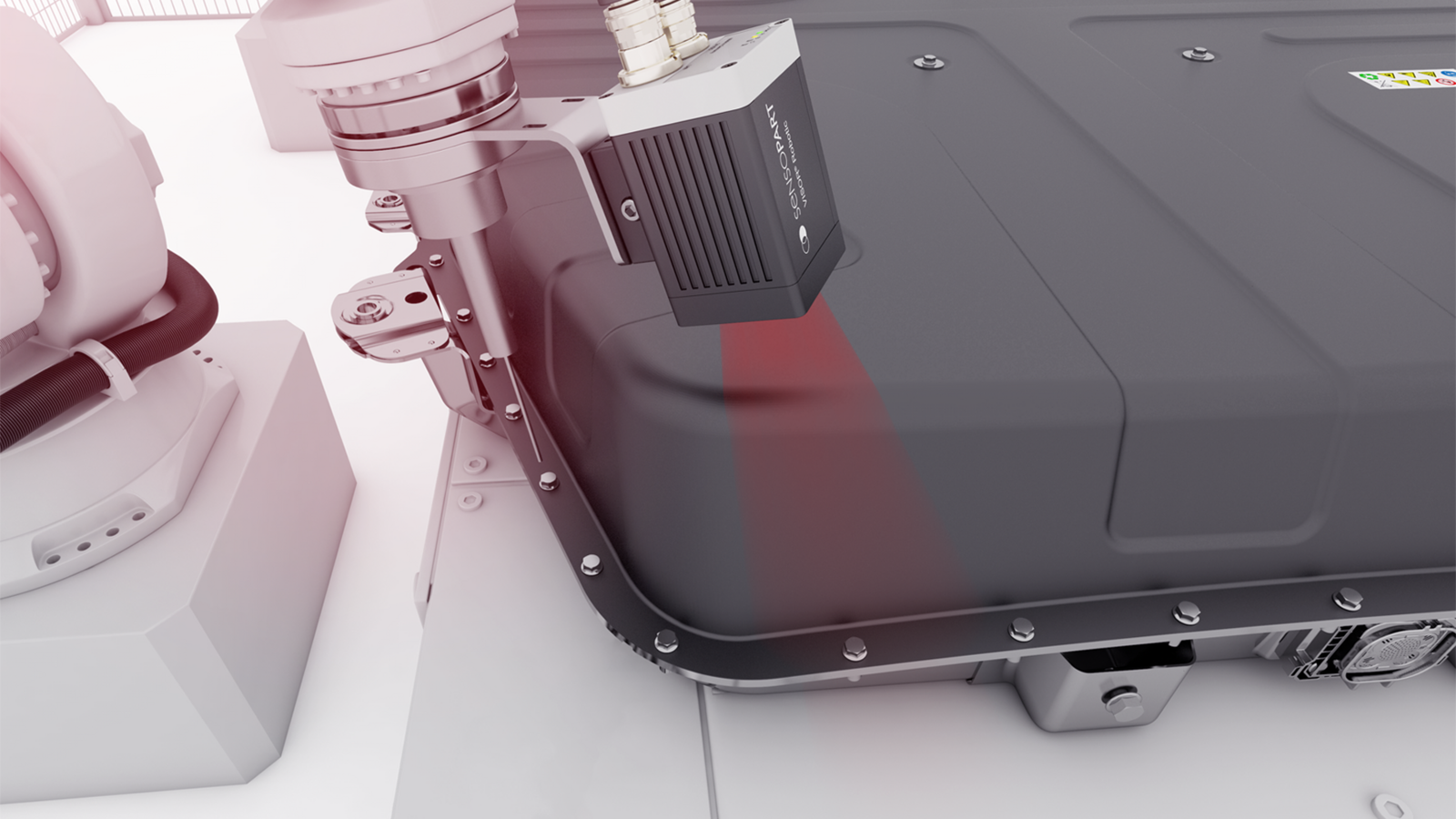
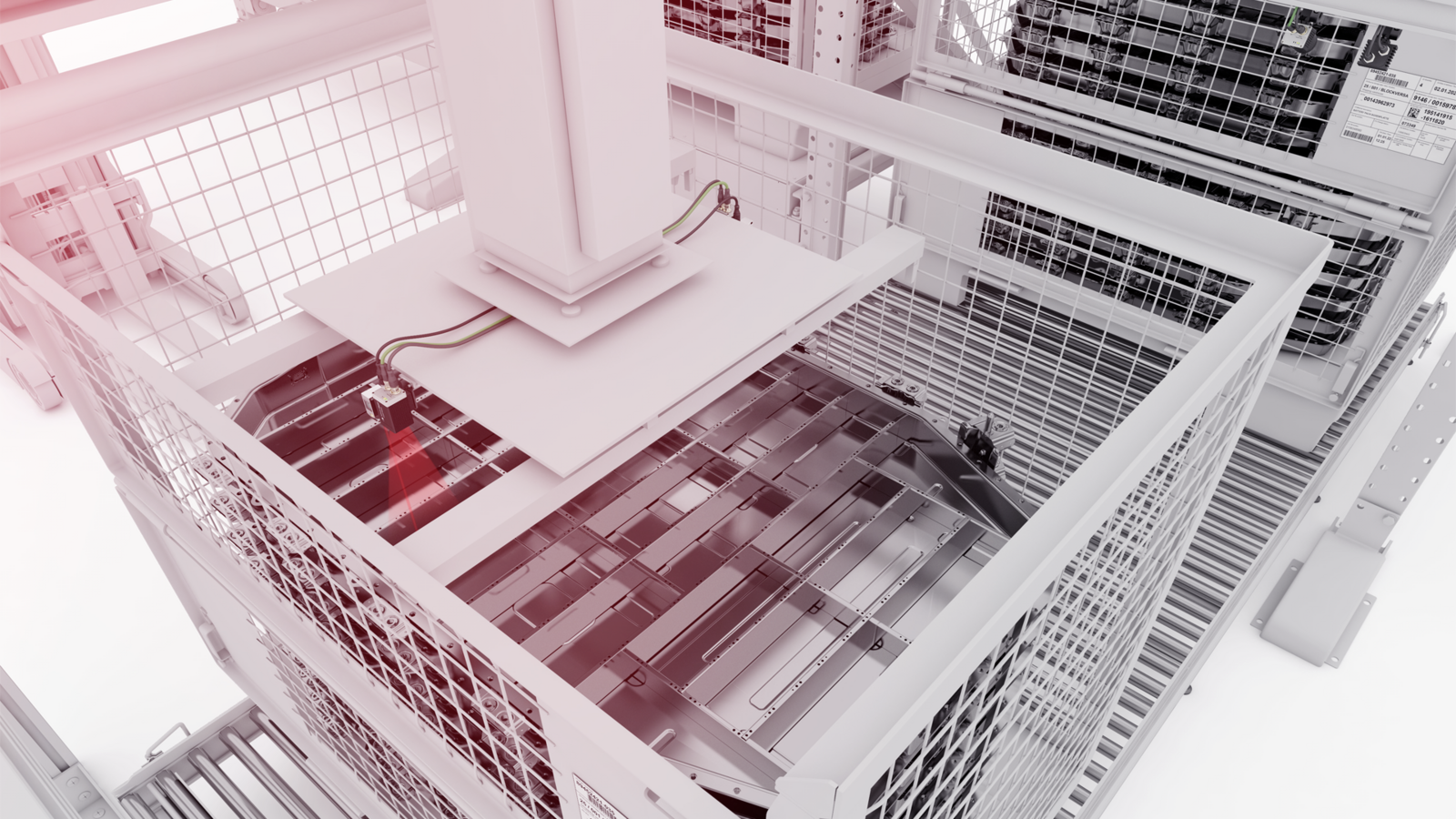
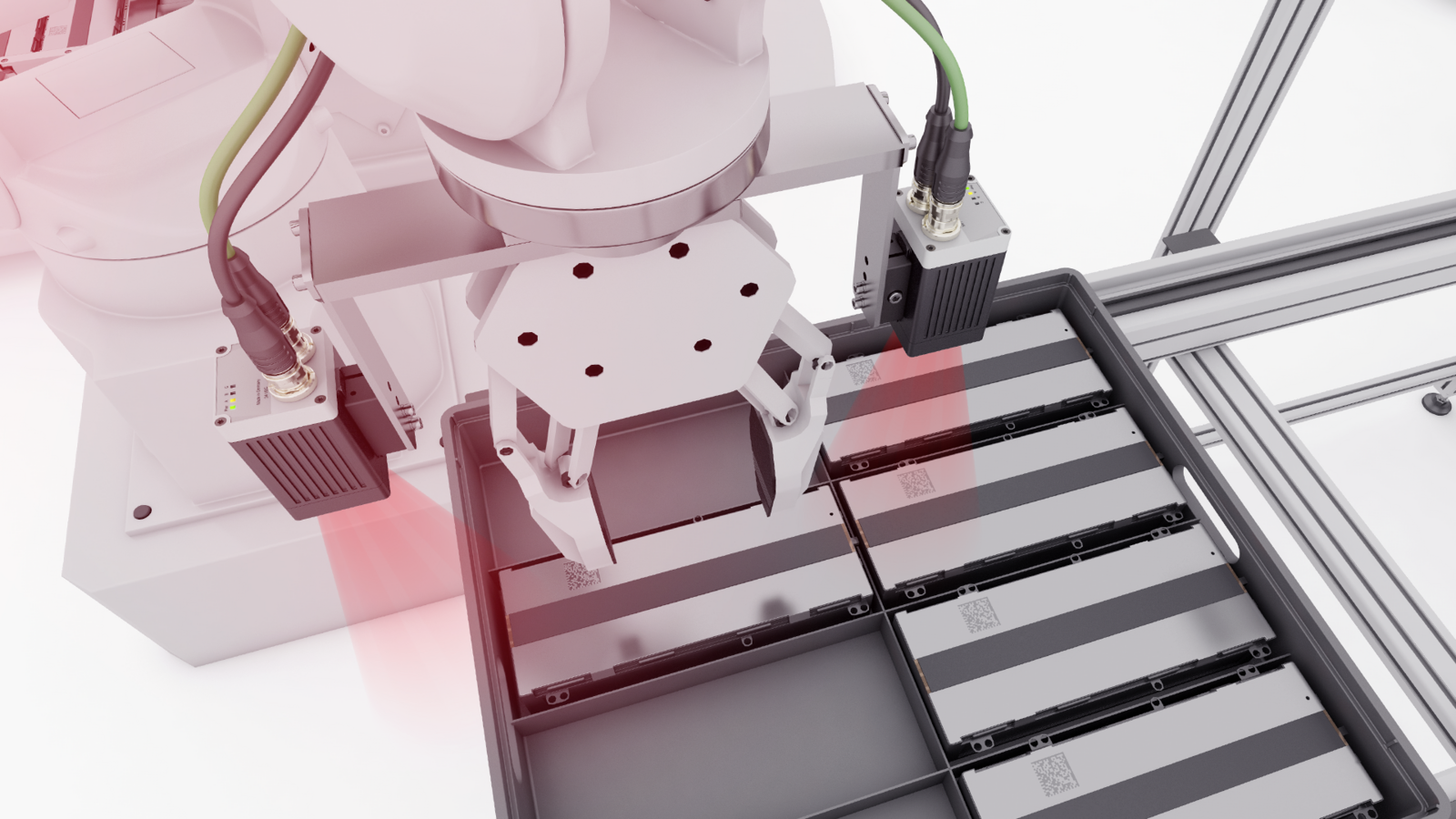
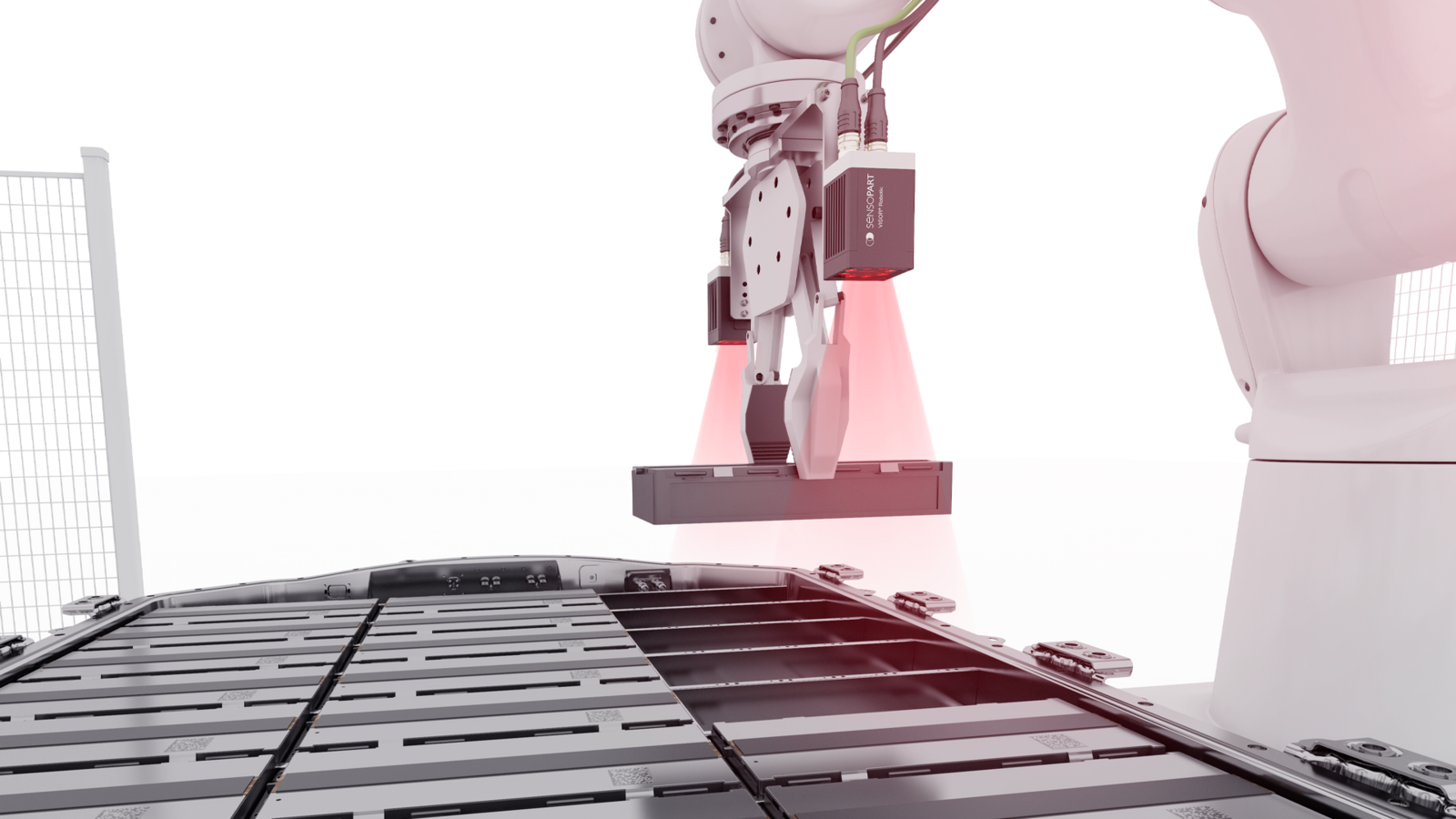
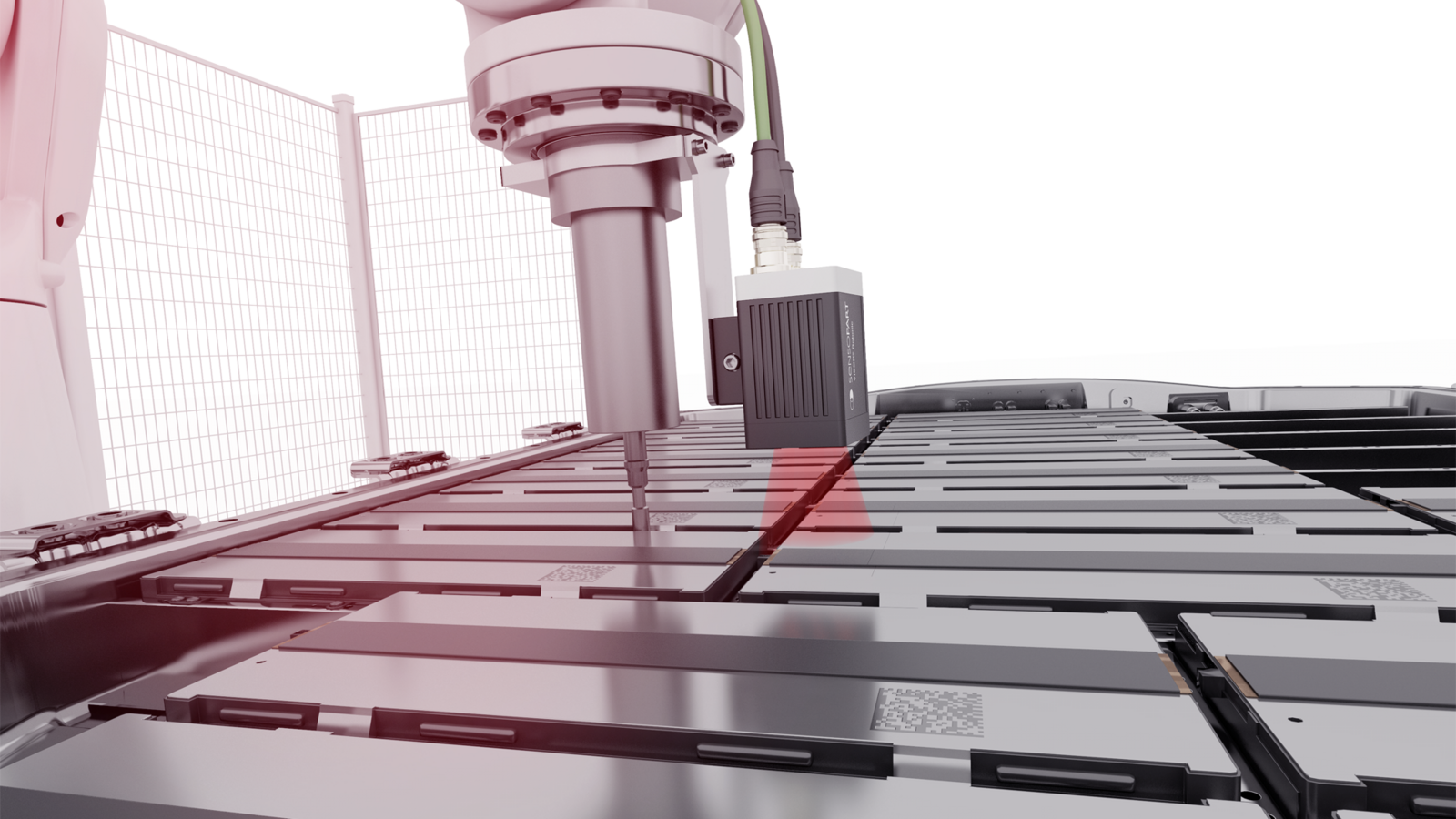
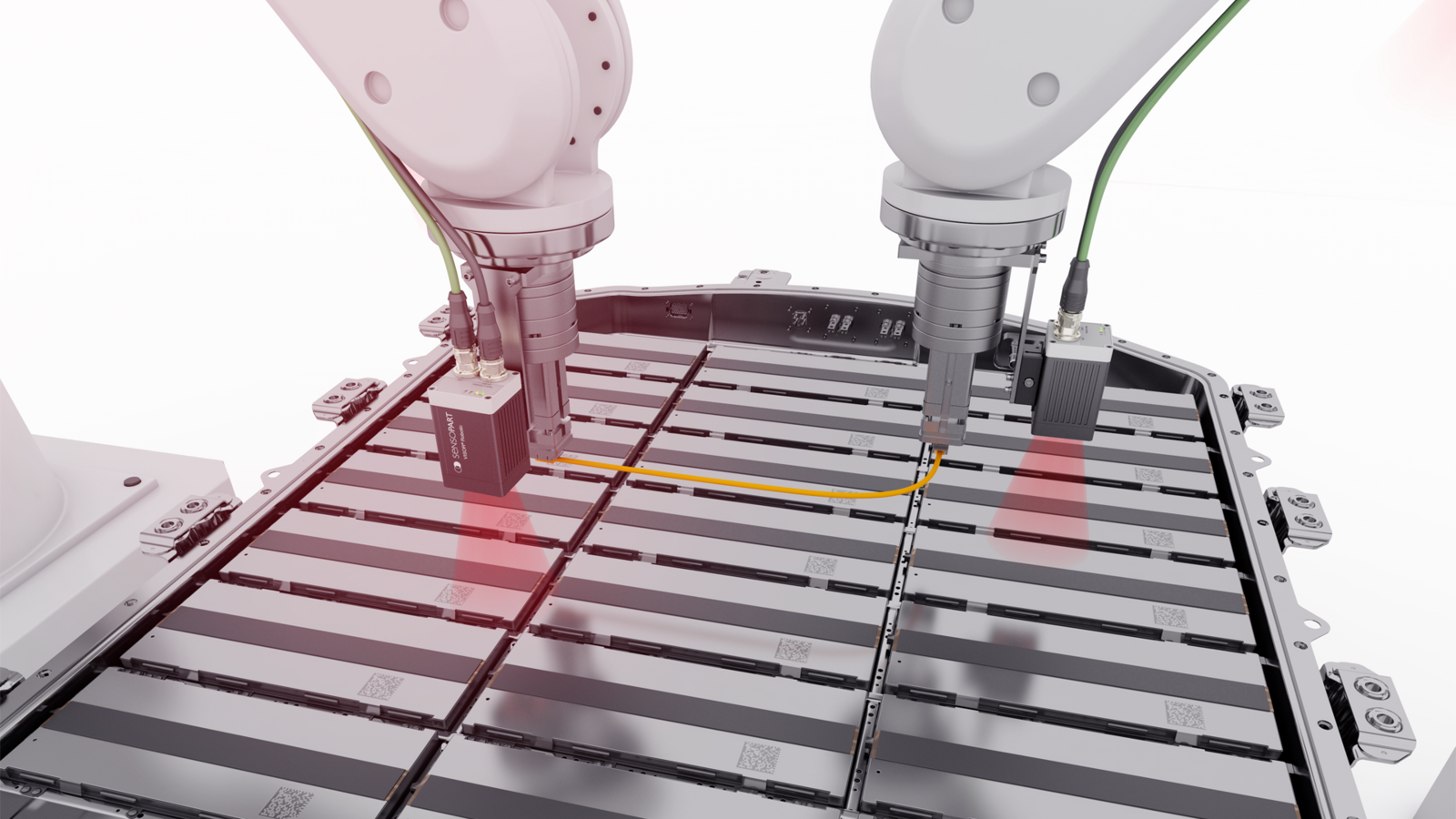
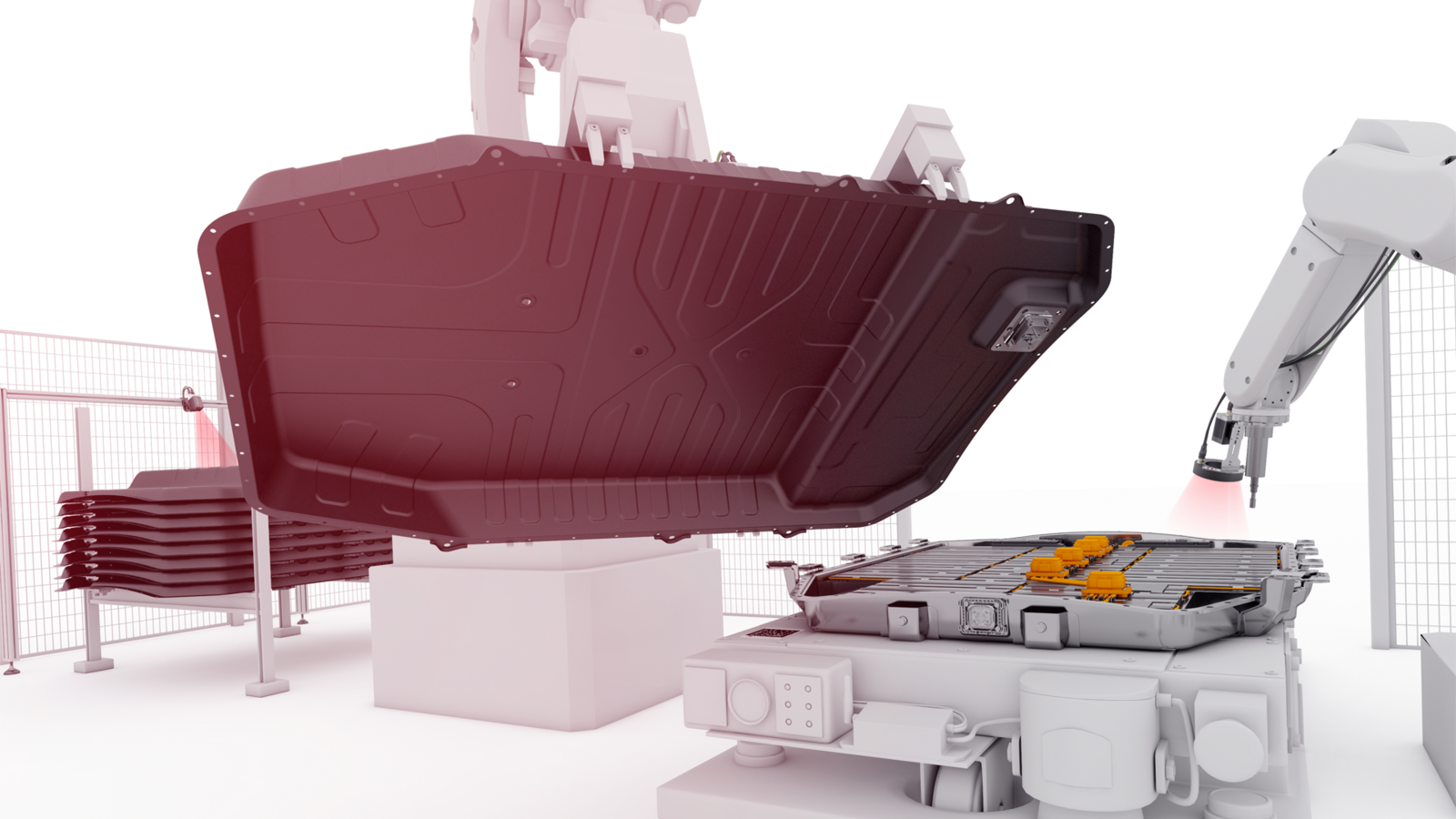
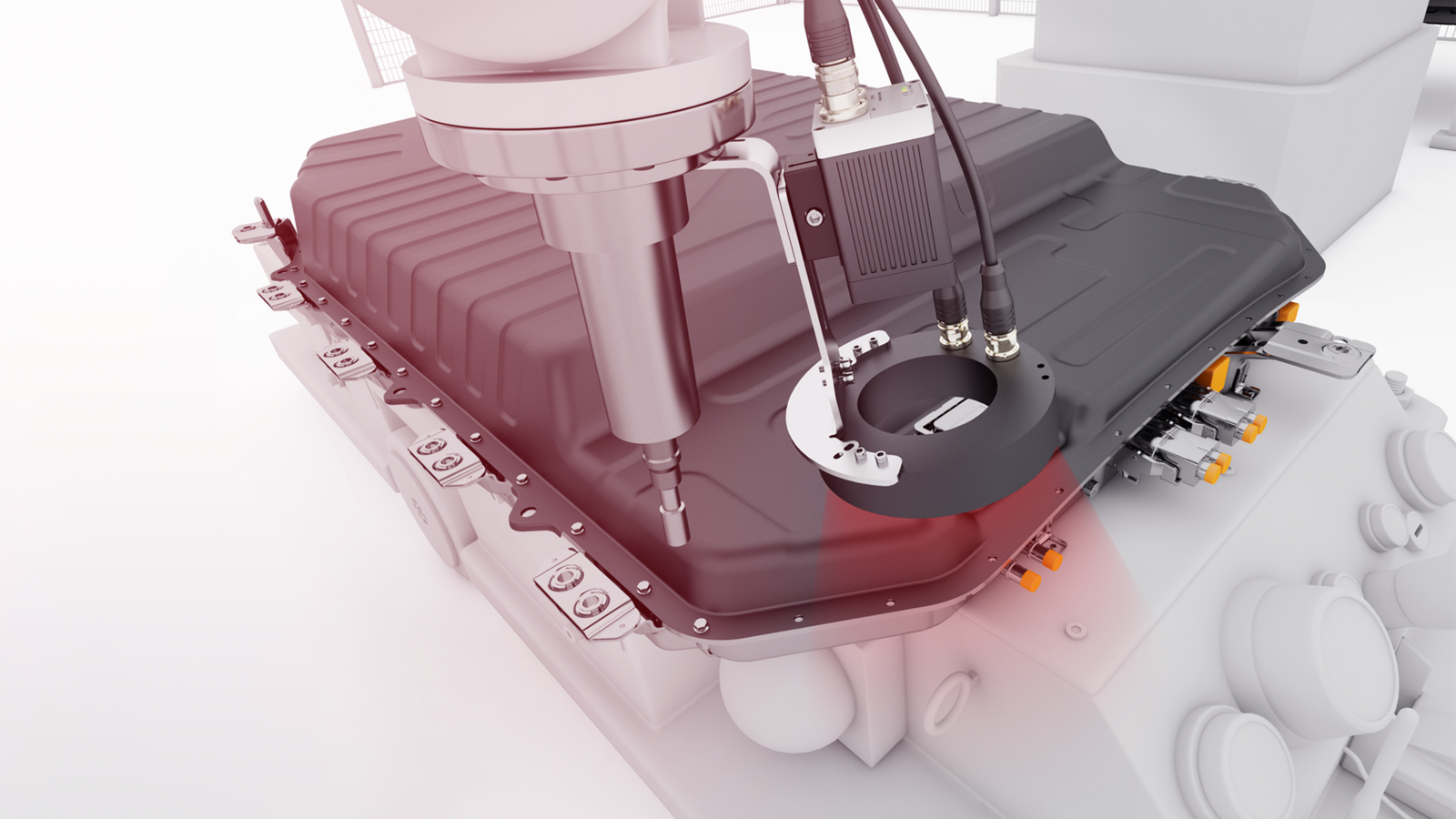